News Center
you can keep abreast of the latest news of NILE and the hot information of the industry.
What is a mine production line? What are the main points of the design of the mine production line?
Time:2021/11/12 News List
Mine production line refers to a production line composed of crushing equipment, screening equipment, grinding equipment, feeders, etc, which are widely used in the production of sand and gravel in quarries in the mining industry. Reasonable mine production line design can make full use of space and make production more smooth. So, what are the design guidelines and key points followed by the mine production line? How can we build a mine production line with "safe production, energy saving, environmental protection, and stable performance"?
Design Guidelines for Mine Production Lines
1. Reasonable layout of the production line, so that the process can be controlled, the operation is smooth, and the operation is convenient.
2. Jaw crushers, cone crushers and other large power-consuming machines are placed as close as possible to the power distribution room and the main control room, which can save cables and reduce line losses.
3. It is recommended that the main control room be close to the unit and build two floors, with the lower level being the machine repair room and tool room, and the upper level being the main control, so that the unit's operating status can be easily grasped at any time.
Seven main points of mine production line design
1. According to the size of the crushed stone and the output of the finished material, determine the type of coarse crushing (jaw crusher or gyratory crusher). When selecting coarse crushing equipment, it is necessary not only to meet the requirements of crushing output, but also to meet the requirements of the largest block (particle size) supplied by the quarry. The feed particle size for coarse crushing is above 500mm, and the discharge particle size is below 350mm.
2. Determine whether the feeder discharges waste according to the mud content of the stone.
3. Add an intermediate silo in the production line design to ensure the continuity of the production line's crushing. The advantage of this is that each section can be produced separately, and the production line of the latter section will not be unable to produce due to the maintenance, overhaul and maintenance of the front-end machinery and equipment, and time-sharing production can also be achieved.Reasonable use of peak and valley electricity prices can save production costs to a certain extent.
4. Determine whether the intermediate silo is placed before the second crushing (cone crushing) or after the second crushing according to the particle size requirements of the finished material. If the site requirements are met, it is recommended to build two intermediate silos. In this way, the work efficiency will be higher and the finished product granularity will be better.
5. Determine the size of the vibrating screen according to the performance of the second breaker. It is recommended to choose a larger vibrating screen as much as possible. The main reason is that the large vibrating screen is relatively clean and has less recycled material, which can improve the working efficiency of the crusher; the second is to reduce The vibrating screen loads and prolongs the service life.
6. Determine the size of the vibrating screen according to the output of the finished material. Choosing a large vibrating screen can strictly control the size of the screen to ensure the quality of the finished material.
7. When the site requirements are met, it can also be used as a finished product silo, which can not only improve the efficiency of loading, but also reduce the cost.
In addition, when selecting equipment, it is necessary to fully consider the matching of technical parameters between all levels of crushers to ensure the quality of product grains and meet the requirements of the best crushing ratio of various types of crushers. The Nile Company has a professional production line design team. Before the production line design, the staff will go to the site to analyze and test the characteristics of the stone, survey the topography and topography, and comprehensively consider the production line investment, production cost, environmental protection and energy saving, and design a complete and reasonable product. Line, and provide technical guidance during the installation process. If you have any machine-related questions, you can ask us for free, and we will provide a full range of services.
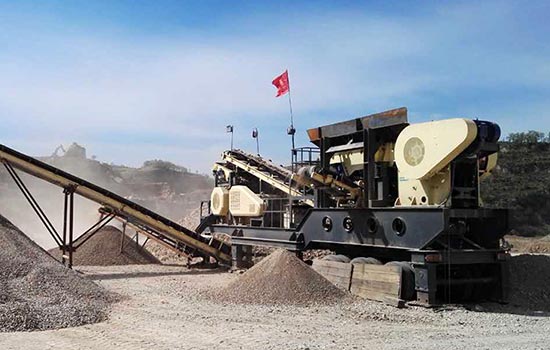
1. Reasonable layout of the production line, so that the process can be controlled, the operation is smooth, and the operation is convenient.
2. Jaw crushers, cone crushers and other large power-consuming machines are placed as close as possible to the power distribution room and the main control room, which can save cables and reduce line losses.
3. It is recommended that the main control room be close to the unit and build two floors, with the lower level being the machine repair room and tool room, and the upper level being the main control, so that the unit's operating status can be easily grasped at any time.
Seven main points of mine production line design
1. According to the size of the crushed stone and the output of the finished material, determine the type of coarse crushing (jaw crusher or gyratory crusher). When selecting coarse crushing equipment, it is necessary not only to meet the requirements of crushing output, but also to meet the requirements of the largest block (particle size) supplied by the quarry. The feed particle size for coarse crushing is above 500mm, and the discharge particle size is below 350mm.
2. Determine whether the feeder discharges waste according to the mud content of the stone.
3. Add an intermediate silo in the production line design to ensure the continuity of the production line's crushing. The advantage of this is that each section can be produced separately, and the production line of the latter section will not be unable to produce due to the maintenance, overhaul and maintenance of the front-end machinery and equipment, and time-sharing production can also be achieved.Reasonable use of peak and valley electricity prices can save production costs to a certain extent.
4. Determine whether the intermediate silo is placed before the second crushing (cone crushing) or after the second crushing according to the particle size requirements of the finished material. If the site requirements are met, it is recommended to build two intermediate silos. In this way, the work efficiency will be higher and the finished product granularity will be better.
5. Determine the size of the vibrating screen according to the performance of the second breaker. It is recommended to choose a larger vibrating screen as much as possible. The main reason is that the large vibrating screen is relatively clean and has less recycled material, which can improve the working efficiency of the crusher; the second is to reduce The vibrating screen loads and prolongs the service life.
6. Determine the size of the vibrating screen according to the output of the finished material. Choosing a large vibrating screen can strictly control the size of the screen to ensure the quality of the finished material.
7. When the site requirements are met, it can also be used as a finished product silo, which can not only improve the efficiency of loading, but also reduce the cost.
In addition, when selecting equipment, it is necessary to fully consider the matching of technical parameters between all levels of crushers to ensure the quality of product grains and meet the requirements of the best crushing ratio of various types of crushers. The Nile Company has a professional production line design team. Before the production line design, the staff will go to the site to analyze and test the characteristics of the stone, survey the topography and topography, and comprehensively consider the production line investment, production cost, environmental protection and energy saving, and design a complete and reasonable product. Line, and provide technical guidance during the installation process. If you have any machine-related questions, you can ask us for free, and we will provide a full range of services.
- Recommended News
- Detailed introduction of Wet pan mill.
- Spiral classifier
- Mobile Trommel Gold Wash Plant
- Discover The Nile's High Performance Wet Pan Mill: Revolutionizing Gold Material Processing
- A Multi-Purpose Grinding Equipment: Wet Pan Mill
- Best Choice for Placer Gold Processing: The Trommel Gold Washer
- Jig Machine in Gravity Concentration for Particles Separation
- A New Type Environment Protection Equipment Fine Sand Recycling Machine
- Hammer Crusher VS Impact Crusher: Technical Comparison and Selection Guide
- Ship directly from Our Factory In Zhengzhou
Recommended Products
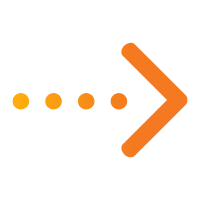