News Center
you can keep abreast of the latest news of NILE and the hot information of the industry.
Phosphate Ore Beneficiation Process
Time:2023/11/14 News List
Phosphorous is an important mineral raw material, and more than 80% of the world's phosphate ores are used to produce phosphate fertilizers and can also be used to make pure phosphorus. The vast majority of phosphorus ore needs beneficiation processing to be utilized. Commonly used phosphorus ore beneficiation processes include flotation, gravity separation, scrubbing desliming, chemical beneficiation and so on.
Phosphate Ore Flotation Method
Flotation method is a very commonly used method in phosphate ore beneficiation. Phosphorus minerals and gangue minerals are closely symbiotic, and the embedded particle size is fine. The flotation method can obtain better flotation indicators.Commonly used flotation processes include direct flotation, reverse flotation, double reverse flotation, etc.
Phosphate Ore Gravity Separation
The phosphate ore gravity separation process is mainly a heavy medium mineral separation method, which uses the different densities of phosphorus minerals and impurity minerals to select a medium with a density between the two, so that one mineral floats in the medium and the other sinks. To achieve the purpose of separation, the gravity separation method has high sorting efficiency and little environmental pollution. It can be used as a pre-selection operation to exclude most of the gangue to improve the indicators of subsequent sorting operations.
Phosphate Ore Scrubbing Desliming
The phosphate scrubbing desliming is a simple process,it is physical benificiation, mainly for weathered phosphate ore. The ore is scrubbed or grounded in the water to remove the surface mud to enrich the phosphorus minerals, but the enrichment of scrubbing method is relatively low.
Phosphate Chemical Beneficiation
Phosphate ore chemical beneficiation method is with the help of pharmaceutical leaching solution to remove the gangue minerals in the ore, mainly carbonate minerals, but the cost of this method is high, only when other beneficiation methods can not get a better concentrate index is selected.
In addition to the above four methods, the phosphate ore beneficiation process also includes roasting method, photoelectric sorting method, etc. However, at present, flotation method is the more effective phosphate ore beneficiation method.
Application of Mineral Processing Equipment in Phosphate Ore
Case 1: 4,000TPD of raw ore
Phosphate Ore
Process: 4,000TPD of raw ore, the crushing process is three sections and one closed-circuit, the coarse crushing in the underground crushing, the surface beneficiation plant is set up in the middle and fine crushing and screening, crushing granularity-15mm, the grade of raw ore phosphorus is 12%, iron is 12%. One section of closed-circuit grinding, the fineness of the incoming materials -200 mesh accounted for 45%, the first selection of phosphorus and then iron, the raw ore after a coarse, a sweep, two fine, concentrate grade 36.5%, phosphate concentrate recovery rate of 93%, phosphorus tailings after a coarse magnetic separation, coarse concentrate regrinding, and then after the second fine magnetic separation, iron concentrate grade 63.5%, iron concentrate recovery rate of 54%. The total tailings are thickened and sent to the tailings storage.
Main equipment: 1 set of PE900*1200 jaw crusher, 1 set of PYY2200/350 cone crusher, 1 set of PYY2200/130 cone crusher, 2 sets of SZZ1836 self-centred vibrating screen, 4 sets of MQG2736 ball mill, 4 sets of 2FG-20Ф2000 spiral classifier, 18 sets of SF8 flotation machine, 3 sets of SF4 flotation machine, 5 sets of JJF4 flotation machine, 2 sets of Ф30m thickener, 1 set of Ф53m thickener. 1 set of CTB1050*2400 magnetic separator, 1 set of CTB1050*2400 magnetic separator, 1 set of CTB750*1800 magnetic separator, 1 set of MQY1530 ball mill, 1 set of GN40 internal filter, 2 sets of 45 square metres ceramic filters, 2 sets of 12m2 permanent magnetic cartridge external filter.
Case 2: 20000 tpd of raw ore
Process: 20000 tpd of raw ore, first magnetic separation of iron and then flotation of phosphorus, iron tailings after grading, regrinding, concentration of phosphorus selection, the fineness of the feeding material is 200 mesh, account 50%. The selected phosphate grade is 2.2%, after one coarse, one sweep, two refined, concentrate grade is 36%, phosphorus concentrate recovery rate is 80%.
Main equipment: 2 sets of Ф8*500 cyclone for tailings classification, 2 sets of 2460 linear screen water screen, 2 sets of Ф80m thickener for pre-flotation concentration, 2 sets of 3245 ball mills for regrinding, 2 sets of inflatable stirring flotation machine: 6 sets of XCF40, 14 sets of KYF40, 4 sets of XCF16, 2 sets of KYF16, 6 sets of XCF8, 6 sets of KYF8, 3 sets of 500m2 of inclined-plate thickener for concentrates concentration, 1 set of Ф15m thickener, and 2 sets of 80m2 disc filters.
Case 3: daily processing of raw ore 4000t / d
Process: daily processing of raw ore 4000t / d, first flotation phosphorus and then magnetic separation of iron, phosphorus tailings directly to iron, raw ore after a closed-circuit milling, into the selection of raw ore fineness is 200 mesh accounted for 40%, the grade of the raw ore is 2.1%, after a coarse, a sweeping, two refined phosphorus selection, phosphorus concentrate grade 33%, phosphorus concentrate recovery rate is 75%.
Main equipment: 1 set of crusher PE750*1060 jaw crusher, 1 set of PYB1750 cone crusher, 1 set of PYD1750 cone crusher, 1 set of 2YA3000*7500 vibrating screen, 2 sets of MQG2736 ball mills, 2 sets of ZKX2148 linear sieve, and 2 sets of inflatable stirring flotation machine: 6 sets of XCF8, 16 sets of KYF8, 6 sets of XCF4, 12 sets of KYF4 for flotation.
- Recommended News
- Mobile Trommel Gold Wash Plant
- Discover The Nile's High Performance Wet Pan Mill: Revolutionizing Gold Material Processing
- A Multi-Purpose Grinding Equipment: Wet Pan Mill
- Best Choice for Placer Gold Processing: The Trommel Gold Washer
- Jig Machine in Gravity Concentration for Particles Separation
- A New Type Environment Protection Equipment Fine Sand Recycling Machine
- Hammer Crusher VS Impact Crusher: Technical Comparison and Selection Guide
- Ship directly from Our Factory In Zhengzhou
- The Introduction of Gravity Separation
- Shaking Table: One of the Main Equipment of Gravity Beneficiation
Recommended Products
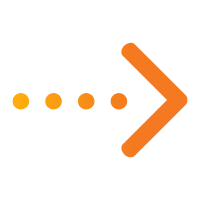